The
Process of Assaying Black Sands
By John V Milewski
Rev. April 10 2008
HISTORY OF MY EARLY BLACK
SAND ASSAYING
These new experiments were first started in late December 2007.
The details of the new assaying process for black sand are given below.
Before I start with these details, I want to comment on a few anomalies
that occurred doing the development of these new and early assay
attempts. I believe that these four anomalies all have the same cause
which is that these new metals are not fully converted from the Ormus
state.
The first anomaly is the disappearance of the first two beads
overnight, the second is that two beads occurred during the cupelling
process and the third is that these assays seem to be producing two
different metal beads in the same assaying experiment—usually, in
conventional assays, they alloy into one compound bead. I have not
heard of any of these things happening before in the typical assay
process.
Finally, the specific gravity of these new "metals" is quite low when
compared to the type of platinum group metals I believe them to be.
My explanation for the observations above is that the metal beads that
formed in two distinct shapes that were separate from each other, in
the bottom of the cupel, were only partly converted Ormus materials.
My understanding of the Ormus atoms is that the outer electrons become
whirlwinds of light and develop a Meissner field which is like a
diamagnetic field that is repelled by all other fields. This repelling
field might cause the different metals to repel each other. So if the
conversion of the Ormus elements to their metallic form was not
complete, then some of this repelling field may have been present. This
might account for the metals separating in the lead solution as these
solutions became saturated and the metal started agglomerating during
the final stages of the cupelling process, when the lead was slowly
disappearing, thus producing two separate beads.
The different shape of these beads, I believe, comes from the natural
crystal structure of these different metals, their relative solubility
in molten lead at the cupelling temperature, and the relatively large
difference in melting points of the two metals. One of the beads was
mostly round like a typical assay bead but it has a rough soccer ball
like surface which I attribute to the fact that high melting point
platinum group metals are not molten at the cupelling temperatures and
therefore precipitate out of solution exhibiting some of their natural
crystal structure which shows up as a rough surface on the metal bead.
See more explanation for this in the Assay method report given below.
The second bead came out looking like a bundle of grapes which are
extremely lustrous and shinny. This grape shape bundle of metal I
believe to be Iridium and the larger soccer ball shape metal I believe
to be Rhodium.
This first batch was finished late at night and I only had time to look
at them under my binocular microscope to see their relative shape and
size. The ball which I believed to be Rhodium was about 1500 microns in
diameter and probably weighted about 15 to 25 milligrams. The grape
bundle which I believe to be Iridium, was about 1100 microns long and
about 300 to 400 microns in diameter with each individual grape being
about 100 microns in diameter.
It was late and I did not take the time to photograph and weight them
individually since I planned to do that in the morning. I put them
together in a small 50 ml size, closed-lid bottle for overnight
storage. In the morning they were gone. I believe that they were not
converted enough to real metal and reverted back into the non metallic
Ormus state as a gas. For more discussion on the idea see an article
about Ormus is a gas see:
http://www.hbci.com/~wenonah/hudson/ormusgas.htm
http://www.subtleenergies.com/ormus/tw/ormusgas.htm
This was very disappointing but I was also running a parallel
experiment using almost the same conditions and would have these
samples in the next two days.
As described in the new assaying process for black sands below, it
takes 4 to 5 firings and cupellings to get the entire yield from one
starting assay run. This run gave five individual beads ranging in size
from 400 microns in diameter to 900 microns in diameter. When
completed, I put all five beads in one cupel and then I added 10 grams
of Silver-free lead and cupelled them together. This time two beads
also formed but they were not separated. They were bonded together and,
under the microscope, looked like a small silver basketball with a
bundle of shinny, silver marbles stuck on the side.
From earlier experiments in 1996, where this same grade of magnetite
was reduced and then run through X-ray analysis, it was determined that
the ratio of Rhodium to Iridium was about five to one in favor of the
Rhodium and that the total amount of these platinum group metals
together could be up to ten percent of the magnetite. See the details
of this data in the report titled Discussions
of X-ray data of reduced Magnetite, by John V Milewski, Revised June
16, 2007
These beads, when fused together, weighed 0.332 grams. That is a super
tremendous yield and represents about ten percent of the starting
magnetite. WOW, WOW. This is unheard of and almost impossible to
believe, except for the fact that the beads are still here, because
this time they did not disappear overnight.
However, this is when the fourth anomaly showed up: I can easily
measure the diameter and weight and calculate the specific gravity of
the new metal. I expected it to come out in the 14.5 g/cc range but, to
my surprise, it came out to be about 8 g/cc. I explain this by assuming
that these beads are still exhibiting some of their Ormus properties
and have not fully gained their metallic weight.
So I am coming to the conclusion that all four of these strange
anomalies, that we see when assaying magnetite black sand, are a
byproduct of this Microwave process. (The Microwave process apparently
does not completely convert these elements from the Ormus state to the
new metallic state.
This Microwave process was repeated again and again and each time two
metals were formed. However, the yields were not as high a before but
still very significant for a black sand assay, and the metal beads
still remain and have not disappeared to date.
The variations in yield may be attributed to the fact that when
assaying in a microwave it is very difficult to control the
temperature; which may vary as much as 50 degrees C from process to
process. When the whole assembly is placed on the carrousel the
temperature is always lower and more uniform and the yield is always
lower.
It is obvious that, for future work, the equipment needs refining as
well as an optimization of the full process; but I thought getting this
out to more skilled processors may help this come about sooner. Since
the metals do show a very reduce specific gravity in the 7 to 8 range
where no platinum group metals come even close, we still have a mystery
and clearly more exploratory work has to be done to understand what is
going on here.
INTRODUCTION TO CURRENT ASSAY METHOD
Using a standard assay for iron oxide on magnetite/black sand does not
work well. The magnetite is too chemically inert to dissolve, to any
relevant extent, in the standard assay flux. As a result, it mostly
remains undissolved and severely thickens up the assay glass so it does
not pour and separate from the lead. This also results in no
significant detectable amount of platinum group metals being extracted
from the black sand ore.
When you use the standard assay process, of about 30 grams of black
sand and 90 grams of flux, you get a relatively smaller lead button
which is about half the expected weight. When you cupel this lead you
get a very small bead that can be seen with a 20 x microscope and which
measures out to be in the 50 micron range. Looking at this bead at a
much high power, one can see an unexpectedly different surface
structure.
I have been doing fire assays for over 30 years now; so I know what
these differences mean.
If the metal you are assaying is either Gold or Silver when the
cupelling is complete you will get a small metal bead. If it is Gold
you have the golden color that is unmistakable. But if it is Silver,
Palladium, Platinum, Rhodium or Iridium the colors are all a silvery
metallic color. With Silver the surface is mirror smooth like a shinny
glass Christmas bulb. The reason for this is that the cupelling
temperature is so close above the melting point of the Silver that it
is essentially coming out in a molten state. However when assaying
platinum group metals that have melting points considerably above the
cupelling temperature then you get a significantly different surface
structure. That is because you are precipitating the metal out of a
saturated solution and its crystal structure begins to show as
irregularities on the surface that make it look more like a soccer ball
with a side growth of the second metal as seen in figures 1 and 2 below:
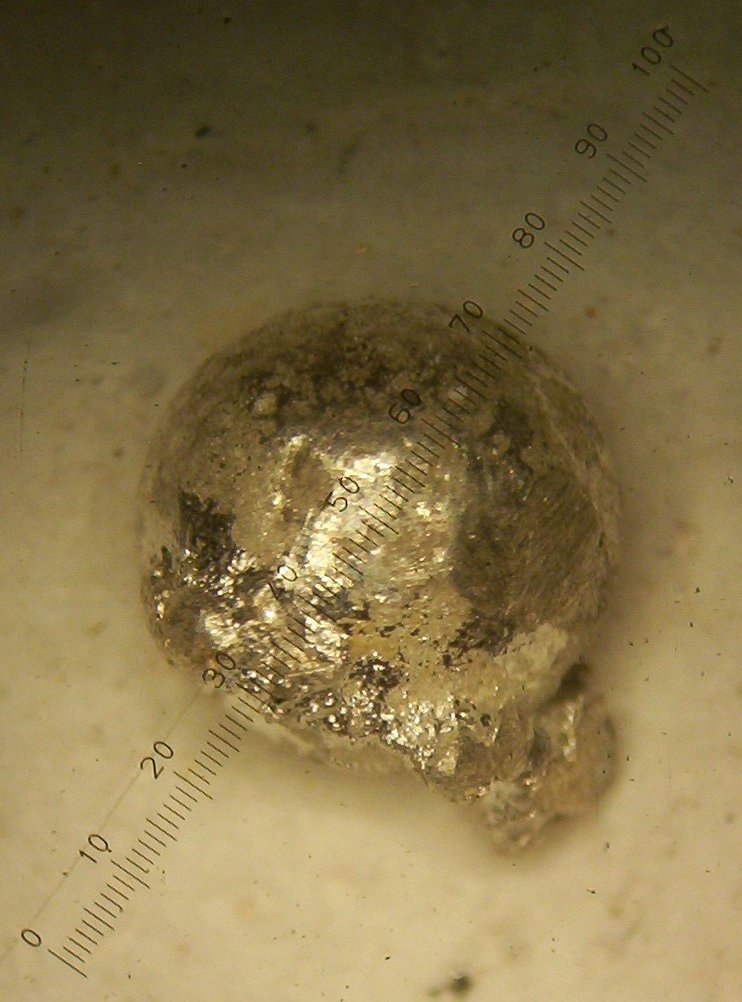
Figure 1
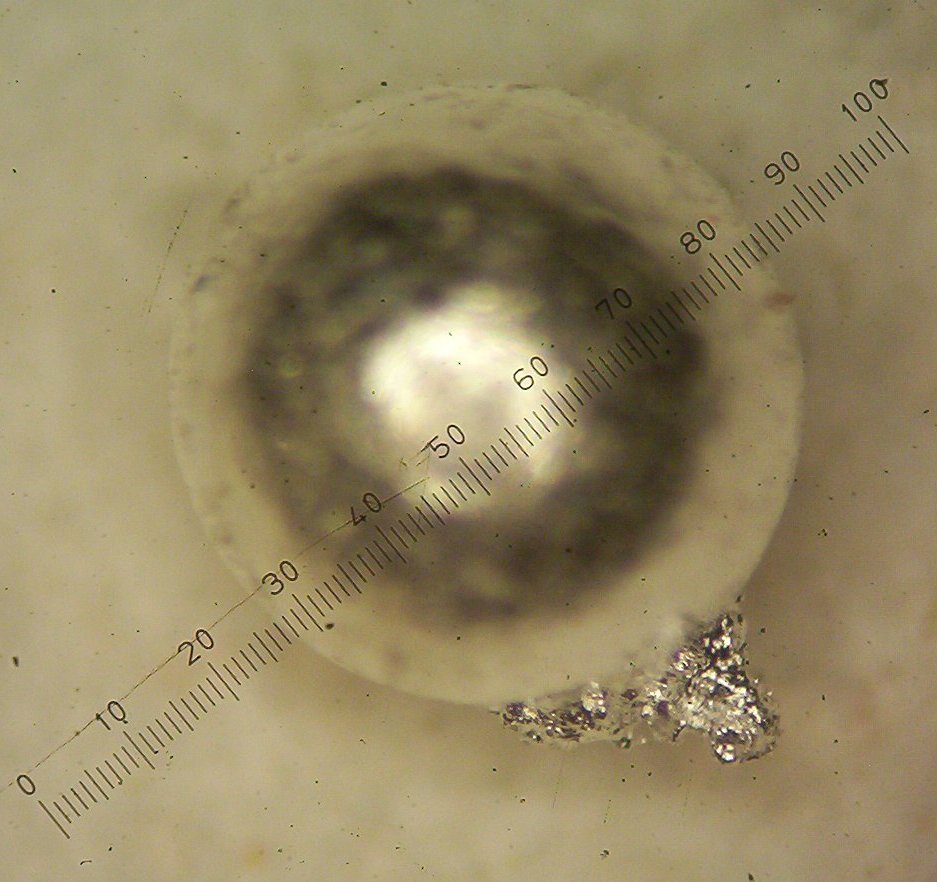
Figure 2
ASSAY PROCESS
Because of the thickening process, as just discussed, 30 grams of
starting ore is clearly too much ore. Also, because of my earlier work
on x-ray analysis of reduced magnetite I became convinced that the
black sand contains a very high percentage of platinum group
elements—in the neighborhood of 10%. (See the separate report on this
below.) This report shows that three grams of black sand would contain
about 0.3 grams or 300 milligrams of platinum group metals which will
be very easy to detect and make a very large assay bead. So my next
assay was to try 3 grams of magnetite with the standard amount of flux.
The glass poured okay with some dissolved magnetite in it and the lead
button came out about standard size—approximately 32 grams. However the
bead size after cupelling was very small only about 100 microns.
Examination of the bead under high magnification did show that this had
a surface structure of the higher melting platinum group metals with
what I call a soccer ball surface as discussed before and shown in
figures 1 and 2 above.
So I started a program of trying different ways to modify the assay
process to get a greater yield. The first modification I made was to
add carbon via charcoal to the assay mix. The reasoning for this is
that at the high temperatures of the assay process the carbon will
reduce the magnetite or iron oxide to form alpha iron. The reasoning
behind this idea is the alpha iron is much more chemically active to
work with that the very chemically resistant magnetite.
So the next assay contained three grams of charcoal plus the three of
magnetite and ninety grams of flux. This gave a bead yield two to three
times larger than the assay run with no carbon but still producing a
very small yield in the range of 0.01 to 0.02 oz per ton. Even so, when
the bead was examined under the microscope it was seen to have the
soccer ball surface typical of a high melting silvery white bead. I
then made a few more runs with more and sometime less amounts of
carbon, all with the same results of a very small bead of a high
melting platinum group metal.
After a few days, at about 4 AM in the morning, the idea came to try
graphite. So my next run was made using this mix: 3 grams of black
sand/magnetite ore, 3 grams of carbon charcoal, 3 grams of graphite and
90 grams of flux. See figure 3 below:
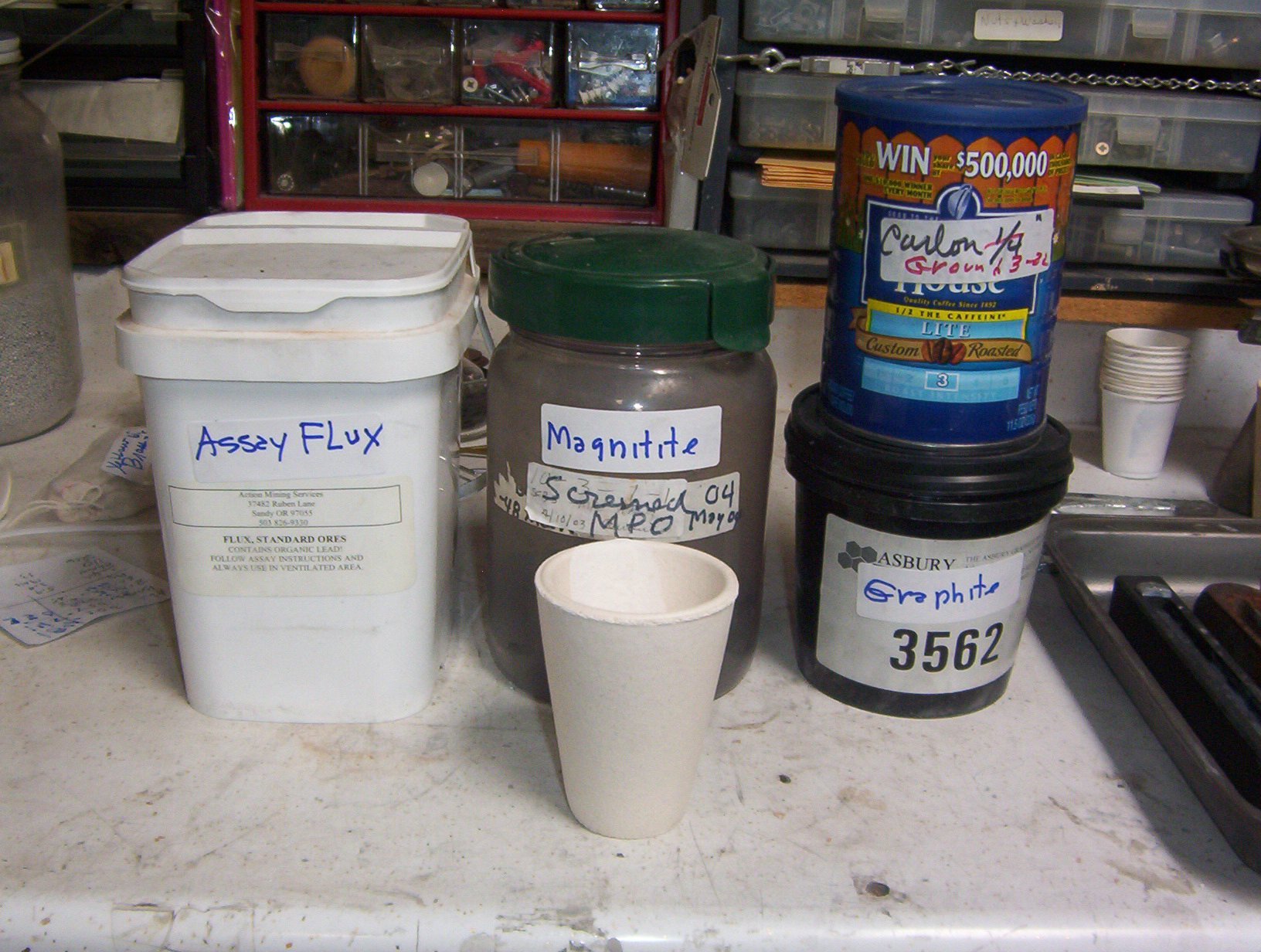
Figure 3
This new mix proved to be very fruitful but at the same time much more
difficult to complete. The graphite made the assay glass very thick and
difficult to process, so during the first pouring only about 1/3 of the
lead came out in the button and the glass was heavily thickened with
the graphite. However, as I said before, this was extremely fruitful,
producing a very large bead that weighed 14 milligrams. Upon
examination of the glass it was seen the each of the graphite flakes
was heavily coated with a myriad of tiny balls of lead. So the next
step was to take the glass filled graphite lead mix and put it in an
open dish and burn off the graphite and collect some more of the lead.
This was done and a second lead button was collected and cupelled
resulting in a very large bead that was almost the same size as the
first bead. This one weighed 13 milligrams.
At this point in the process there still was a lots of lead coated
glass, which I believed still contained a lot of platinum group metals
in the lead and unconverted ormus elements in the glass. A second assay
like run was made on this residual mix with 10 grams of lead and 25
grams of boric anhydride added to make the mix more fluid during the
pouring. This assay process was also a success. The lead button
produced another large bead; this time about 11 milligrams. See all
three beads in figure 4 below:
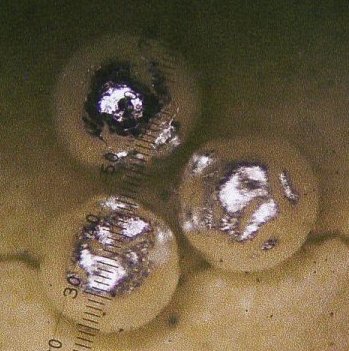
Figure 4
When I added all three beads together and cupelled them with ten grams
of lead, a large bead was produced as shown earlier in figure 2. This
bead now produced a very significant yield of 38 milligrams which, in a
standard assay, would represent about 38 oz of platinum group metals
per ton. This is a very high number but remember that this assay was
run on only 1/10 of the standard amount of ore. So, correcting for
this, we now have a yield of about 380 oz per ton of high melting
temperature, silver colored, platinum group metals.
A positive identification of these metals has not yet been obtained but
from my experience I strongly believe them to be Rhodium and Iridium. A
close look at the photos in figures 1 and 2 shows a round ball with a
rough surface, which I believe to be Rhodium, and a side growth, with
many very small balls attached to the side of the bigger bead, which I
believe to be Iridium.
From my earlier work, as reported in the x-ray testing done several
years ago, it was calculated that the ratio of Rhodium to Iridium is
about 5 to 1, and this looks like the approximate amount of the two
different looking metals found in the combined metal bead that came
from the final cupelling in the process I just described.
I believe that the much higher melting point of the iridium causes it
to saturate and precipitate sooner into the smaller crystal balls
making it look different when compared to the larger Rhodium ball which
comes out later in the cupelling process.
So, in conclusion, a process has been developed for assaying black
sands by using a much lower amount of ore, processing it in a microwave
and adding materials to the flux to help convert the platinum group
elements, that I believe are in the Ormus form in the black sand, into
metals which only show up as metals in the in the final cupelling stage
of the assay process.
MICROWAVE PROCESS
The microwave process that I am using is described in the following
photo sequence. Figure 5 below shows the insulation blocks all cut to
6x6 inch squares. The thicker 2 inch blocks have a 3 inch diameter hole
in the center that holds the crucible.
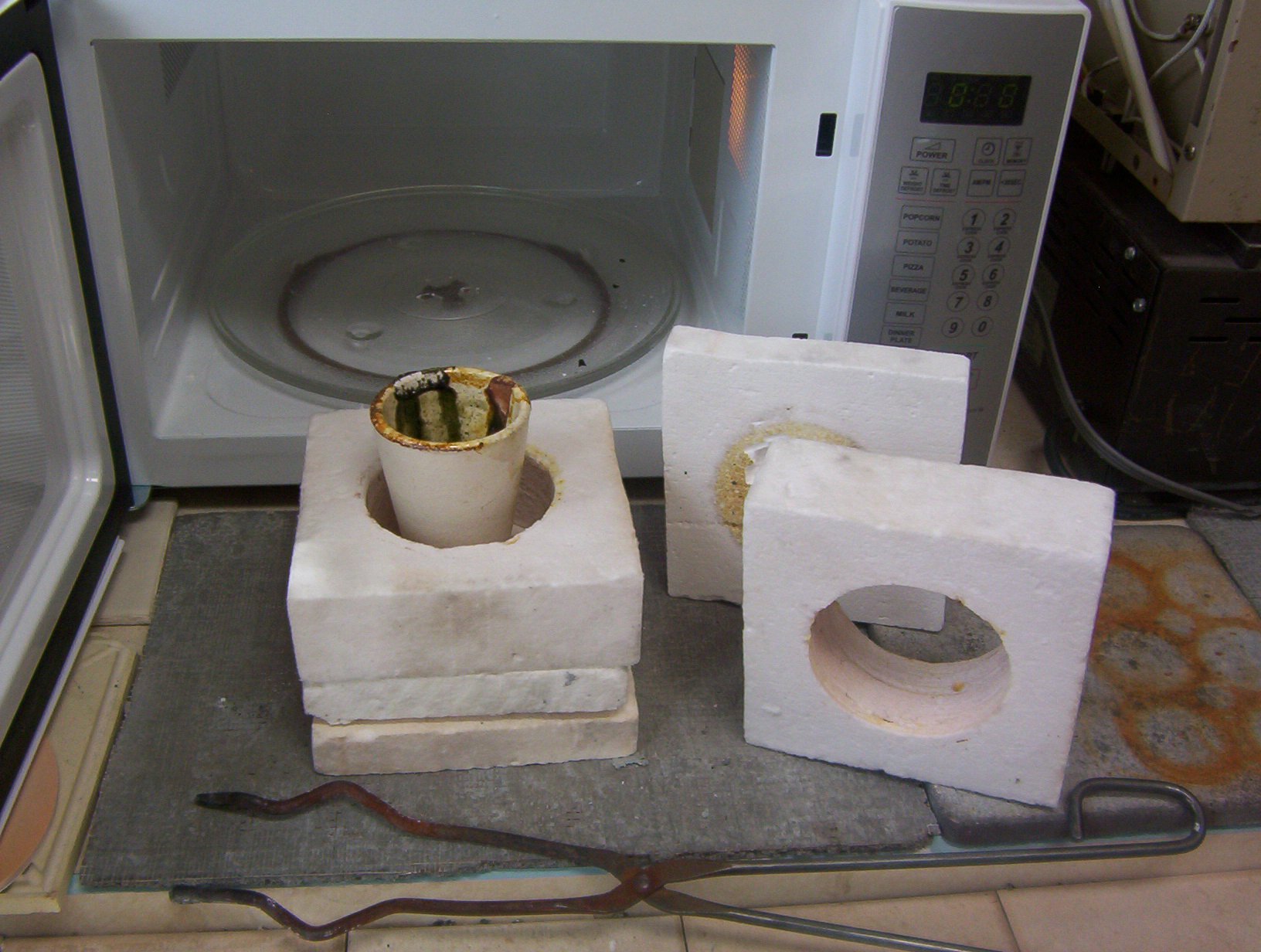
Figure 5
In the microwave processing, these are covered top and bottom with a
one inch thick insulating block as seen fully assembled into the
microwave furnace in figure 6 below:
Figure 6
Figure 7 shows the 15 gram size clay crucible loaded with the 90 grams
of flux, ore and additives—ready to go into the insulation assembly:
Figure 7
Figure 8 shows the assembly after it was taken out of the furnace, for
a look at the temperature, after 5 minutes of processing in the
microwave at power setting 10. It is just starting to get red in color
and exhibit some melting.
Figure 8
Figure 9 show the same crucible after 20 additional minutes at power
setting 8. It is fully melted with a red to orange color:
Figure 9
The unit was then left in the microwave for an additional 10 minutes at
power setting 7 to allow more mixing and processing to take place. At
this time the unit is taken out of the furnace and the crucible is
poured into a cast iron cone mold so the lead and glass can be
separated as illustrated in figure 10 below:
Figure 10
Figure 11 shows the lead button at the bottom of the glass cone and
figure 12 shows it separated after being weighed:
Figure 11
Figure 12
It then it goes into the cupelling furnace as seen in figure 13 to
complete the process:
Figure 13
Finally the platinum group metal beads are collected as seen in the
earlier figures 1 and 2.